CNC lathe processing
Ordinary: It is often used in actual use to manually measure the relative position of the CNC lathe. Taking the z-direction tool as an example, move the tool after installing the tool, cut the right end face of the workpiece by hand, and then retract the tool along the x direction to set the distance between the machining origin and the right end face. Input the CNC system to complete the cutting process of the tool.
Change: The tool nose detection system is realized. Depending on the set speed, the cutting edge approaches the contact sensor and sends a signal. In tool setting, the spindle, tool holder, contact sensor, etc. are mainly used. It can automatically complete the tool setting, which is conducive to improving the machining accuracy, and is currently being widely used.
External: The essence is to measure the distance between the virtual tool point and the table reference point in the X and Z directions. Use the auxiliary function of the external machine tool to create good conditions for subsequent processing and production on the off-campus machine tool. In practice, after installing the CNC lathe, input the corresponding compensation number to the tool length at any time to meet the needs of workpiece processing and production, and lay the foundation for the smooth progress of the follow-up work.
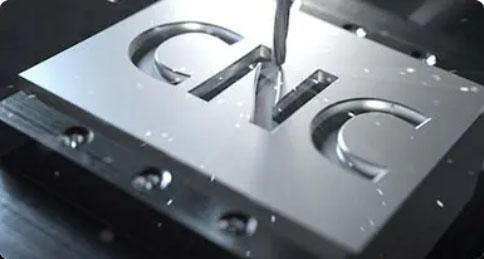