Precision parts processing
This paper analyzes the market demand and process concept of precision parts, combines the skills and problems in actual processing (limited to the scope of clamp work), and discusses the solutions and skills of related problems in precision parts processing, so as to improve precision parts. quality, improve the contradiction between market supply and demand, and promote the development of a technological and intelligent society.
In actual production, the structure of each part may be very different, which greatly increases the difficulty of processing. But if you observe carefully, you can find that the basic geometric composition of the parts is nothing more than an outer circle, an inner hole, a plane, a thread, a tooth surface, a curved surface, etc., so as long as you master the processing of these shapes, the difficulty of precision parts processing is also can be significantly reduced.
In the process of precision parts processing, the reasonable selection of positioning datum determines the quality of the parts, and whether the dimensional accuracy and mutual position accuracy requirements of the parts can be guaranteed, as well as the processing sequence arrangement between the surfaces of the parts are very important. big impact. If the workpiece is installed with a fixture, the selection of the positioning datum will also affect the complexity of the fixture structure. Therefore, the choice of positioning datum is a very important process problem in the machining of precision parts.
Now, mechanized and automated production has been achieved in some of the production processes, so the use of automated processing systems can automatically monitor its operating status, and automatically adjust its parameters when subjected to external interference or internal excitation to achieve the best state and Self-organizing ability, thus greatly improving the roughing and finishing efficiency on the premise of ensuring the machining accuracy.
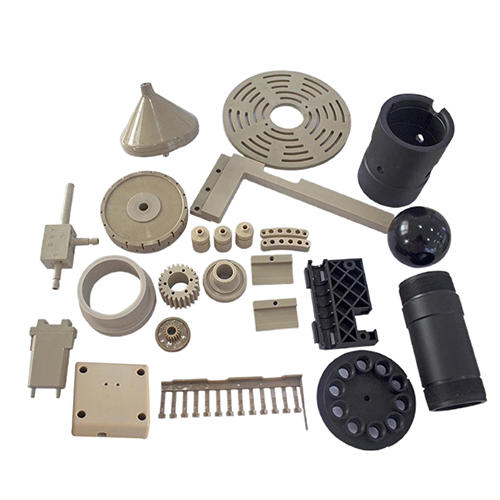