What are the characteristics of aluminum alloy CNC machining?
1. Aluminum alloy has low hardness
Compared with titanium alloy and its quenched steel, the hardness of aluminum alloy is lower, of course, the hardness of heat-treated or die-cast aluminum alloy is also very high. The HRC hardness of ordinary aluminum plates is generally below HRC 40 degrees. Therefore, when machining aluminum alloys, the load of the tool is small. And because the thermal conductivity of aluminum alloy is better, the cutting temperature of milling aluminum alloy is relatively low, which can improve the milling speed.
2. Aluminum alloys have low plasticity
Aluminum alloy has low plasticity and low melting point. When machining aluminum alloys, the sticking problem is serious, the chip evacuation performance is poor, and the surface roughness is relatively high. In fact, the processing of aluminum alloy is mainly due to the poor effect of sticking and roughness. As long as the two major problems of sticking the knife and the quality of the machined surface are solved, the problem of aluminum alloy processing will be solved.
3. The tool is easy to wear
Because of the use of unsuitable tool materials, when machining aluminum alloys, the tool wear is often accelerated due to problems such as sticking and chip removal.
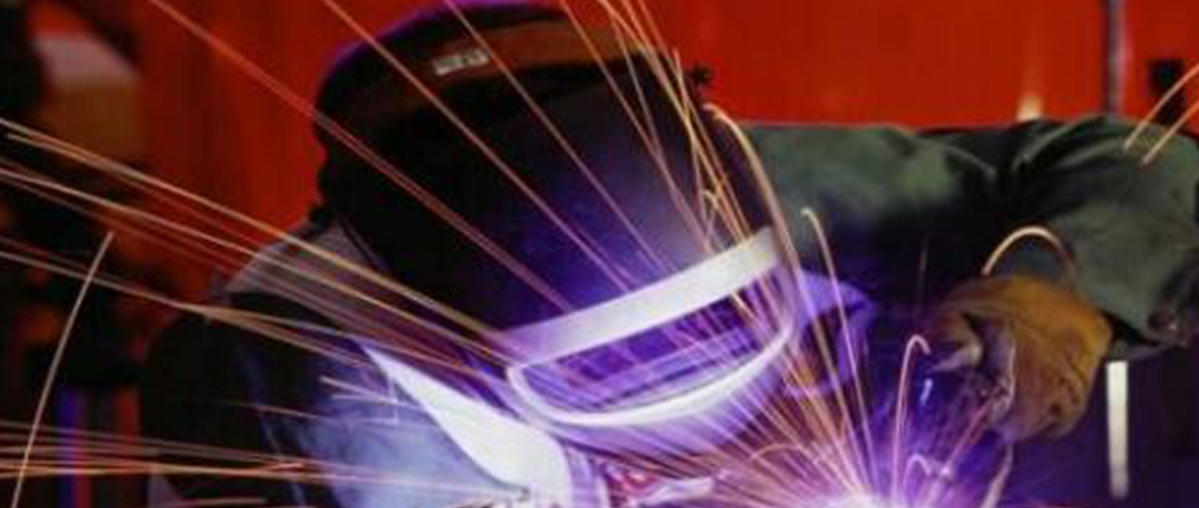