First, the type of mold used is important. There are single cavity molds and multiple cavity molds. Typically, single cavity molds are used for lower-volume batches. This type of mold has a single cavity that produces one part per injection cycle. However, some materials require special molds. Some of the more common materials include PC, PEEK, polystyrene, and polyether imide.
Other types of molds include pin gates, tab gates, and tunnel gates. These gates allow the resin to enter the cavity. Pin gates are suitable for parts that are free of vestige, and tab gates are ideal for cosmetic parts that are free of texture. Tunnel gates are generally used in cosmetic parts that are made with additives.
During the injection molding cycle, a heated mold will add heat to the liquid plastic. This process, known as cavitation, is used to increase production. A mold can also be made to produce multiple parts at the same time. However, it is important to consider the size of the mold, as well as the number of parts that you need to produce. If the mold is too small, you may not be able to produce all of the parts you need.
If you are considering using injection molding, you should also consider the costs of testing, marketing, and assembly. Also, consider the size of your project, and how many parts you will need to produce in order to break even. You may find that you will need to increase the price of your parts, or change brands. The cost of injection molding can also increase depending on the size of the part. You may also need to add a secondary process to produce the part. For example, some parts need a machining operation or need to be glued together.
Injection molding is a highly automated process. It requires a high degree of precision and fast cycle times. However, it is not recommended for large, complex, or intricate parts. For these reasons, injection molding is not appropriate for large pieces. The parts need to be small, and there is little design flexibility.
The temperature, pressure, and speed of the injection molding process are also important factors. If not enough pressure is used, the cavity may not pack completely, and the part may not be able to be formed. If you have any concerns, speak with your mold designer.
For example, some plastics require additional treatments such as ultrasonic welding or laser engraving. These treatments can help to produce a specific surface finish or color. You may also want to consider using a material with a higher melt flow index. This can help to compensate for some of the defects caused by shrinkage.
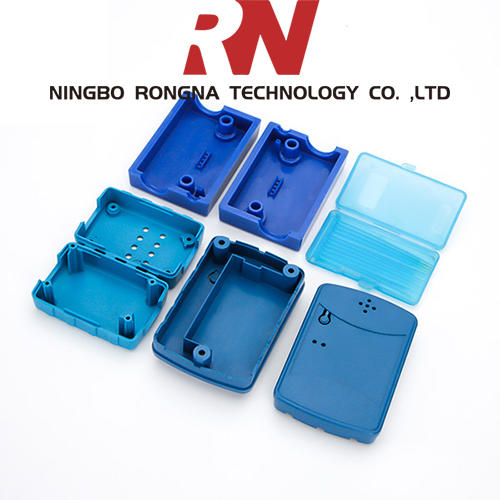