Creating a prototype plastic injection mold is a great way to test a new product design. It can save you time and money and help to identify design issues early in the development process. It can also serve as a bridge tooling solution to allow you to transition to production tooling.
Prototype plastic injection molds are built quickly and efficiently. They are used to test the form, fit and functionality of a part in the development process. They can also be painted to mimic the look of a finished product. The results are a great way to verify market interest before launching a new product. They also help to show stakeholders that the product can succeed in the marketplace. They can also serve as marketing tools before the final production part becomes available.
Prototype plastic injection molds can be produced in a variety of materials. Most commonly, the tooling is made from hot plastic. Other materials include aluminum and steel. Aluminum can be an ideal tooling material for prototypes, but it can be difficult to achieve industry standard finishes. Steel, on the other hand, can be more expensive and take a longer turn-around time to produce.
Prototype plastic injection molds can be used to test form and functionality, and can help to detect design flaws early in the development process. They can also help to identify design issues before committing to expensive production molds. They can also help to test fit and function, and can be used as a bridge tooling solution to allow manufacturers to transition to production tooling.
Prototypes are also useful for testing designs in the real world. They can be used for marketing purposes before a final production part is available, and can help to convince stakeholders that the product can succeed in the marketplace. It can also help to show the handling of technicians and manufacturers in the design and manufacturing process. They can also be used to provide written instructions and pictures for instructional manuals. They can also help to show needed steps added to later processes, thereby maximizing part quality.
Rapid tooling is a good option for orders of 100-2,000 units. It can be a cost-effective option if your product will be used in a high-volume manufacturing environment. It can also be a cost-effective option if you have strict appearance and functionality requirements. Despite its cost-effectiveness, rapid tooling cannot produce the volume of parts required for mass production tooling. However, the cost of producing a single-digit batch of parts is often less than the cost of reworking production tooling to accommodate changes later in the production process.
Rapid tooling is also helpful to the process engineer who is looking to gauge the efficiency of the manufacturing cycle. It can help to eliminate unanticipated line shutdowns because of defects. A rapid prototype can be created within a few sample cycles. It can be used to test form and functionality, as well as manufacturing errors. It can also be used to determine whether the design is feasible for mass production.
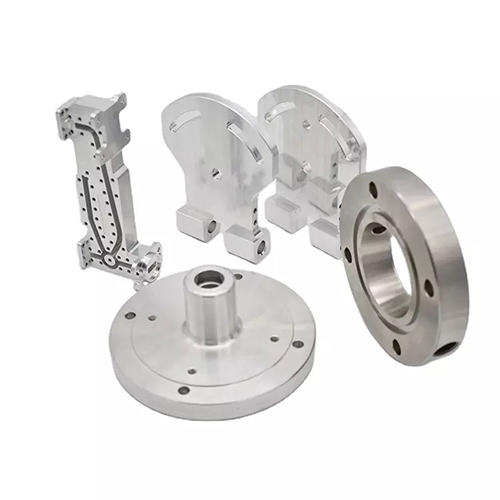