Aluminum alloy CNC machining
In addition, some ions will react with the rust inhibitor of the aluminum cutting fluid, reducing the rust resistance and stability of the cutting fluid, such as calcium and magnesium ions. Therefore, try to choose dilution water with less hardness, or soften the diluted ion-exchange water to ensure the use effect and life of the cutting fluid.
In addition to the daily maintenance of cutting fluid, the maintenance of cutting fluid for CNC machining of aluminum alloys also needs to pay attention to the following points:
1. Filter
Due to the stability of the reaction of aluminum alloy aluminum soap, the cutting fluid is easily damaged under alkaline conditions, and the aluminum scraps, aluminum scraps and cutting fluid should be filtered out immediately to avoid re-reaction and affect the use effect and life of the cutting fluid. The aluminum scraps ground during the grinding process are small and light, and it is difficult to continue to precipitate. If it is not filtered or is not sufficiently filtered, the aluminum scraps processing area will be taken away with the cutting fluid circulation system, and the scratched surface will affect the gloss of the processed surface.
2. ph value
Since the aluminum cutting fluid is very sensitive to the pH value, the pH value of the aluminum cutting fluid should be checked regularly, and if any abnormality is found, it should be adjusted in time. Use ph to control at 8-9 ph value, so as to avoid excessive corrosion of the workpiece or too low ph value to make bacteria multiply and affect the stability and performance of the cutting fluid.
3. Regularly add new programs
It not only ensures the good lubricity of the cutting fluid, but also ensures the good anti-rust and anti-corrosion properties of the cutting fluid, and prolongs the service life of the cutting fluid.
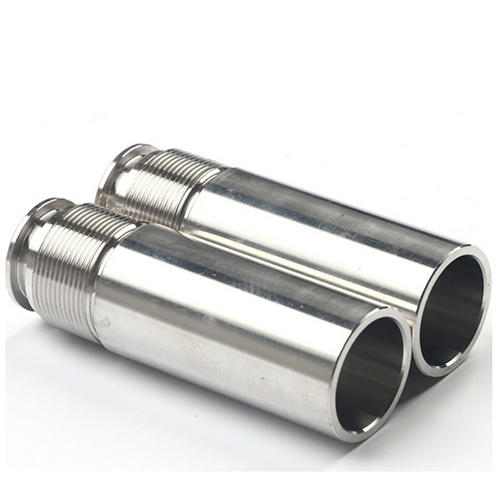