Some common types of plastic prototype materials include plastic injection molding, CNC machining, and vacuum casting. All these techniques allow you to create visual and functional models of your product. You should choose the method that best suits your needs. You should also choose a company that specializes in your specific needs. You should consider the materials that you will be using, the level of detail that you are looking for, and your budget before deciding on a provider.
The most cost effective way to create a visual plastic rapid prototype is to use 3D printing. This process has a wide variety of benefits, and it is usually the best choice if you are working on a short production run. This type of plastic prototyping also allows you to quickly create movie props, car interior panels, and more. It also offers a number of finishing options that you can choose from.
If you need a functional plastic prototype, you will need to choose a method that can create the exact geometry and surface finish that you want. Some methods can take up to a week to complete, and some aren't flexible enough to handle urgent deadlines. The best method will depend on the type of material and part you are trying to make.
During the manufacturing process, the material is supported by a powder. This is important because it helps to create a strong agglomerate. You can also choose to process the inner parts separately. CNC machining is another excellent option, and it is cheaper than other methods. However, this method is not very flexible, so you may need a high-level design before you can make the most of it.
Another method is SLS 3D printing. This process allows for smooth surfaces and high-definition. It has a minimum wall thickness of 0.04" (0.010mm). You can also print miniatures and props with this method. You should expect to pay a little more for a long-run production, though.
Another excellent method is laser cutting. This method is incredibly fast, and it can be used for urgent deadlines. Depending on the size of the part, you can pay anywhere from $75 to $1,000 for a plastic rapid prototype. This method also has a high risk of defective parts, so it is best to hire an experienced fabricator to do the job.
Vacuum casting, or silicone molding, is another rapid prototyping process. It is a three-step process that duplicates dozens of plastic parts. You can choose from a variety of materials, and it is the fastest method of mass-producing a plastic prototype.
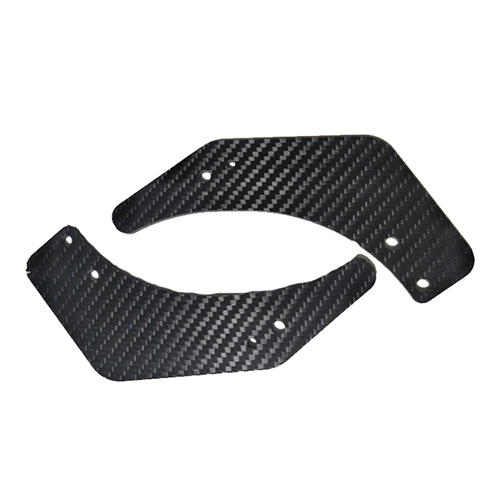