Whether you're creating a one-off prototype or a large production run, CNC Machined Parts can be an effective way to make a wide range of products. This process begins with the design of a solid part in CAD, which is then converted to a format that can be processed by a CNC machine. CNC machining is used in several industries, including aerospace, defense, transportation, medical, and electronics. These industries require highly accurate parts. A wide range of shapes and standard parts can be created, as long as they are optimized for the CNC process. The design process is critical to producing the highest quality parts possible.
There are several key design considerations that can make the process easier and more accurate. Besides the obvious considerations such as length and thickness, there are other factors that can impact machining. Small features and thin walls can reduce machining time and cost. The shape and build of the part also play an important role in determining its accuracy.
The height and width of protruding features are also important considerations. In general, the height of these features should be no more than four times the width of the part. If the feature is longer than this, it is difficult to machine and can be damaged by the vibrations of the cutting tool. Likewise, if the feature is shorter than four times the width of the part, it is also difficult to machine.
Tight tolerances should also be considered when designing CNC machined parts. These tolerances benefit both the part and the process as a whole. They help ensure that the part will fit properly and can reduce the number of setups that are required for machining. This decreases the amount of time it takes to machine the part and reduces re-aligning time. However, tight tolerances also add to the cost of machining the part.
If the part has a blind hole, it should be designed so that it will need only one setup. This saves a lot of time and money. It also reduces the risk of tool hanging, which can damage the parts.
Deflection and vibrations from the tool are also important considerations when designing CNC machined parts. A proper cavity depth helps prevent tool deflection and vibration. Most CNC machining shops have machines that can machine cavities as small as 2.5 mm. However, designers must keep the cavity depth at least four times the width of the part. This will prevent the tool from hanging and increasing vibrations.
If the part is shaped or formed like a dovetail, it is important to add clearance for the tool. Dovetail cutting tools are generally 45 or 60 degrees. This angle is used to define the feature size of the dovetail.
In addition to tight tolerances, it is also important to avoid undercuts. This is especially true when it comes to the design of internal parts. Undercuts can be extremely difficult to machine, especially if the protruding section is tall.
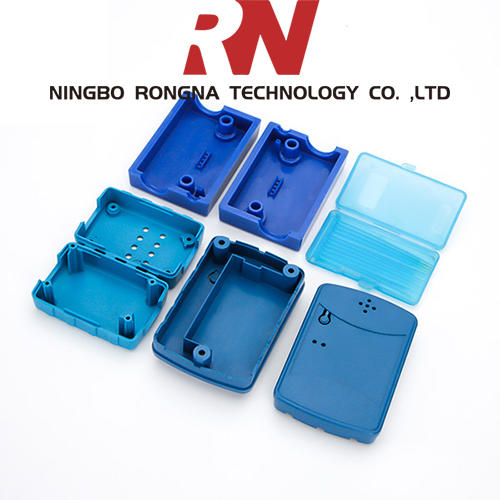