The advantages of aluminum alloy processing are:
1. Easy to process. After adding certain alloying elements, a forged aluminum alloy with excellent forging performance or a deformed aluminum alloy with good working plasticity can be obtained.
2. Good electrical and thermal conductivity. Aluminum's electrical and thermal conductivity is second only to silver, copper and gold.
3. High strength. Aluminum and aluminum alloys have high strength. After a certain degree of cold working, the strength of the matrix can be strengthened, and some brands of aluminum alloys can also be strengthened by heat treatment.
Fourth, the density is small. The density of aluminum and aluminum alloys is close to 2.7g/, which is about 1/3 of iron or copper.
Aluminum alloy processing
Five common problems in aluminum alloy processing:
1. There are rotten teeth, sticking to the knife, and the surface finish of the processing is not up to standard
Aluminum alloy is soft and has a low melting point, so problems such as rotten teeth or sticking of the knife are prone to occur in poor processing environments. In addition to changing the processing parameters, such as avoiding medium-speed processing that is easy to stick to the knife, both lubrication and cooling properties should be used. Better cutting fluid.
Second, the non-processed surface is moldy
Most of the problems in aluminum alloy machining are caused by cutting fluids. The insufficiency of the design of the cutting fluid product itself means that problems are unavoidable in the processing process. The non-processing of die-casting aluminum alloys has a sensitive response to the corrosion inhibition ability of cutting fluids, and mildew is one of its manifestations. Mildew of aluminum alloy is usually caused by insufficient aluminum corrosion inhibition ability of cutting fluid and insufficient microbial control ability of cutting fluid. When mildew occurs, it is necessary to start from the improvement of the corrosion inhibition ability of the cutting fluid and the improvement of the storage method after machining.
3. Residues on the machined surface affect post-cleaning
Aluminum alloys generally need to go through a cleaning process after machining. If the cleaning ability of the aluminum alloy cutting fluid is not good, residues will be produced on the aluminum alloy machined surface, which will affect the appearance or later processing such as coding. It is usually related to the design of the emulsification system of the cutting fluid product and the cleaning process.
Fourth, a large amount of foam is generated during processing
Cutting fluid foam is generally avoided as much as possible in the machining process. Insufficient cooling caused by foam and severe tool wear can lead to poor machining results and reduced machining efficiency. Especially with the update of the machine tool, the five-axis machining center has higher requirements on the foam of the cutting fluid. The cutting fluid with insufficient anti-foaming and defoaming ability will cause the liquid level to rise abnormally, trigger the liquid level alarm, and stop the normal operation of the machine tool. The improvement of the foam performance of cutting fluid can not only be solved by adding defoamer, but should be optimized from the system design of cutting fluid products.
Fifth, the cutting fluid has a short service life
In the process of machining aluminum alloy workpieces such as pistons, gearbox cylinders, etc., there is a common problem of short life of cutting fluid. The service life of the cutting fluid not only involves the frequency of tank replacement and the cost of investment, but also affects the quality of processing and the working environment on site. The service life of the cutting fluid is mainly reflected in the stickiness and corruption of the tank fluid after a period of use. The stickiness makes it difficult for the aluminum chips to separate from the surface of the aluminum parts, resulting in indentations, and corruption reduces the machining quality of the cutting fluid and deteriorates the working environment on site. Stickiness is related to the selection of emulsification system in cutting fluid design and the ability to control microorganisms. Corruption is related to the introduction of microbial nutrients in cutting fluid and the selection of bactericidal and bacteriostatic system. Of course, it is also related to the use and maintenance of cutting fluid on site. related.
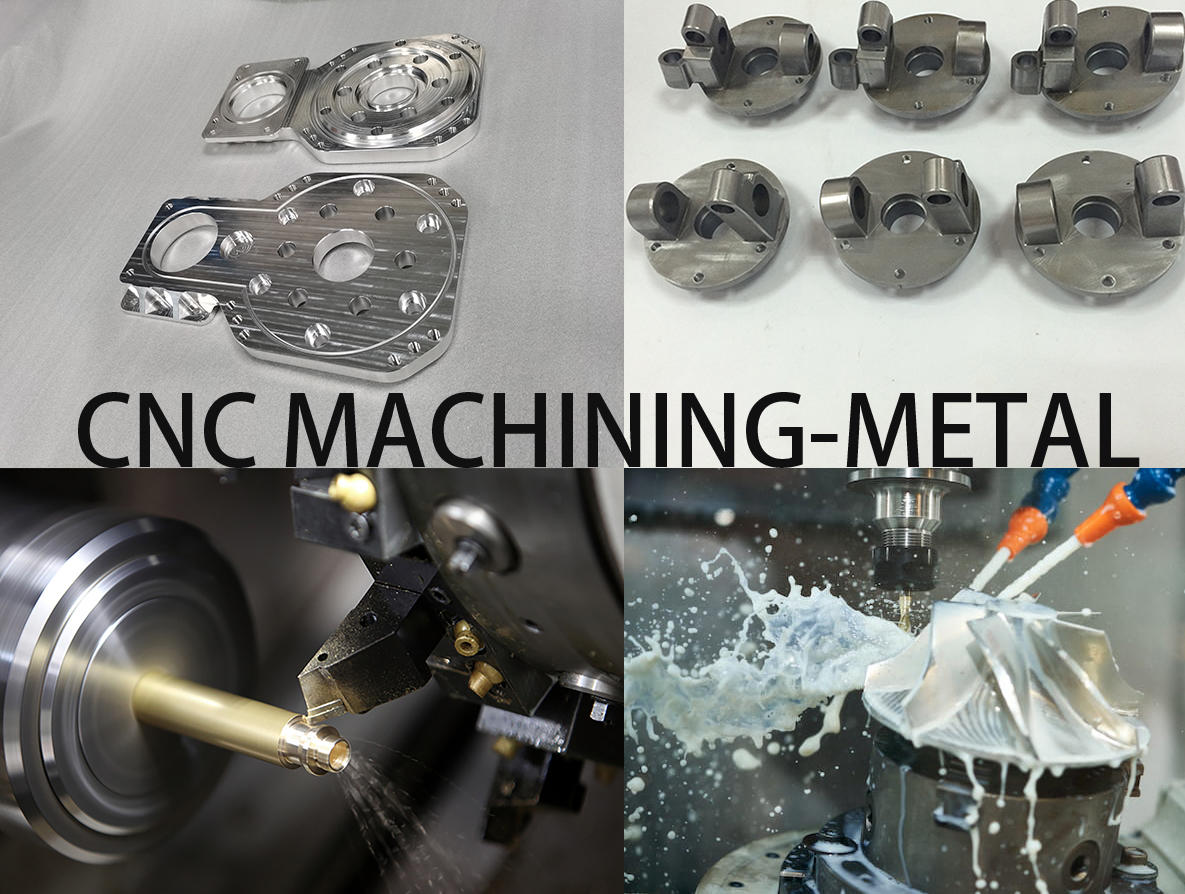